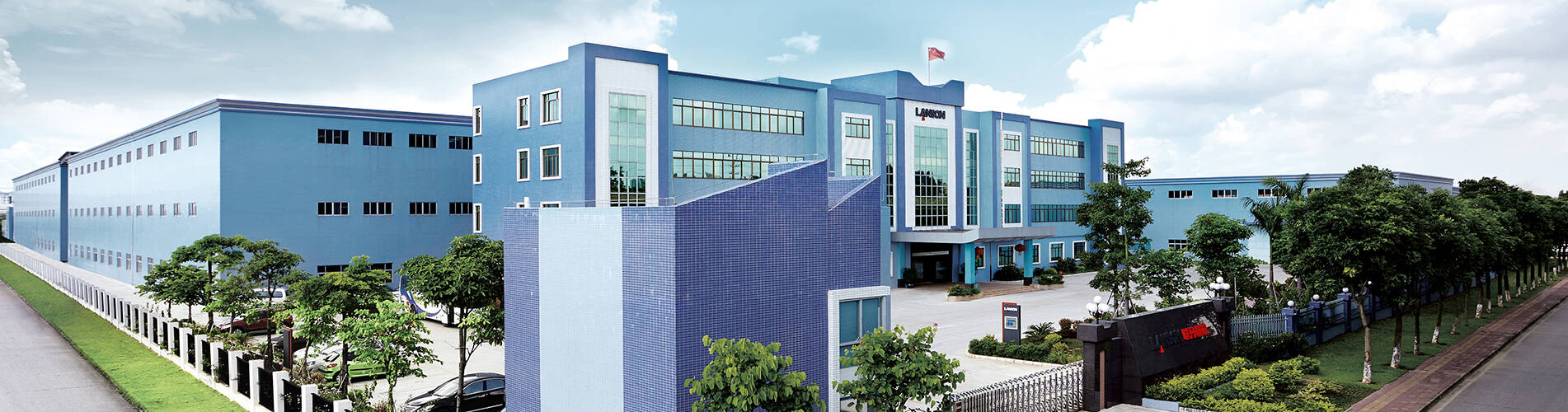
Setting injection molding process
Injection molding process set seven factors to consider are as follows:
(1)reduction of thermoplastic plastic molding shrinkage and calculation as mentioned above, in the form of the influencing factors of thermoplastic plastic molding shrinkage is as follows.
1) plastic varieties
Because there is crystallization in the process of thermoplastic plastic molding forms of volume change, internal stress is strong, frozen inside the plastic residual stress is large, sex factors such as molecular orientation, so compared with thermosetting plastic shrinkage is bigger, wide range of shrinkage and clear direction, also after molding shrinkage, shrinkage rate after annealing or wet processing generally are larger than the thermosetting plastic.
(2) plastic parts features
When forming the molten material in contact with the cavity surface outer cooling form low density solid shell immediately. Due to the thermal conductivity of the plastic, plastic lining, formed by the slow cooling contraction of high-density solid layer. So the wall thickness, slow cooling, high density layer thickness contraction. In addition, the presence of insert and insert layout and quantity are directly affect the direction of material flow, density distribution and the size of the shrinkage resistance, etc., so the characteristics of the plastic parts had a greater influence on the size and direction of contraction.
(3) inlet form, size and distribution
These factors directly affect the direction of material flow, density distribution, pressure feeding function and forming time. Direct inlet, the inlet cross section big (especially the cross section of the thicker) is narrow, but the direction is large, short inlet width and length of the directivity is small. From the inlet near or parallel to the direction of material flow of contraction.
(4) the molding conditions
High mold temperature, melt material slow cooling, high density, shrinkage, especially for crystal material with high crystallinity, volume change is big, so the shrinkage is bigger. Mould and plastic parts inside and outside cooling temperature distribution and density uniformity, also directly affect the shrinkage of each part size and direction. In addition, keep the pressure and time is influence on shrinkage, pressure, time long, narrow, but the direction. High injection pressure, melt material viscosity difference is small, interlaminar shear stress is small, large elastic rebound after demoulding, reason can also be appropriate to reduce shrinkage, high temperature, shrinkage, but the direction is small. When molding accordingly adjust the mold temperature, pressure, injection rate and the cooling time and other factors can also be appropriate to change plastic shrinkage. Mold design according to the scope of all kinds of plastic shrinkage, wall thickness and shape, size and distribution, the inlet forms according to the experience to determine the shrinkage rate of plastic pieces of each part, and then to calculate the cavity size. For high precision plastic parts and difficult to grasp the shrinkage rate, general appropriate design mold in the following way.
(1) the plastic outer diameter smaller shrinkage rate, Canon take larger shrinkage rate, in order to test after correction of leeway.
(2) test to determine the gating system form, size, and molding conditions.
Reprocessing (3) to the post-processing of plastic parts size changes to determine the size (measurement must be within 24 h after demoulding).
(4) fixed mold contraction according to the actual situation.
5. Try mould and can properly change process conditions, slightly amended shrinkage value to meet the requirements of plastic parts
(2) the liquidity
Thermoplastic liquidity size, general but from the size of molecular weight, melt index, Archimedes spiral flow length, apparent viscosity and flow ratio (flow length/plastic pieces of wall thickness) and a series of index are analyzed. Small molecular weight, broad molecular weight distribution, the regularity of the molecular structure is poor; High melt index, long length of spiral flow and apparent viscosity, flow ratio of the liquidity is good. Plastic must check the specification of the same name to judge whether its liquidity is suitable for injection molding. According to the requirements of mould design commonly used plastic liquid can be roughly divided into three categories.
1) good liquidity PA, PE, PS, PP, CA, poly methylpentene 4.
(2) liquid medium polystyrene series numerical, such AS ABS, AS, PMMA, POM, polyphenylene ether.
(3) illiquid PC, hard PVC, polyphenyl ether, polysulfone, aromatic sulfone, fluorine plastics.
All kinds of plastic liquidity, but due to the forming factors of main factors are as follows:
(1) temperature
High temperature increases liquidity, but different plastic also each have differences, P S type (especially impact resistance and higher MFR), PP, PA, PMMA, modified polystyrene (such AS ABS, AS), PC, such AS CA plastic liquidity larger changes with temperature. For PE, POM, the temperature increase or decrease in smaller influence on its liquidity. So the former in the molding time adjust temperature to control liquidity.
(2) the pressure
Injection pressure is molten material shear effect, also increase the liquidity, especially sensitive, POM, PE, so forming time adjust injection molding machine pressure to control liquidity.
(3) the mould structure
Gating system of the form, size, layout, design of cooling system, the molten material flow resistance type (such as surface roughness, feeding section shape, thickness and cavity exhaust system) and other factors directly affect the molten material within the cavity of the real liquidity, that prompted the molten material to reduce the temperature, increase liquidity resistance of the liquid is reduced. Mold design should be according to the liquidity of the plastic used, with reasonable structure. When molding are also can control the material temperature, mold temperature and injection pressure, injection speed and other factors to properly adjust the filling conditions to meet the needs of the molding.
(3) the crystalline
Whether appear when thermoplastics by condensation phenomenon can be divided into crystallization type plastic and an amorphous type (amorphous) plastic two categories. Crystal phenomenon is the so-called plastic by molten state to condensation, the molecules move by the free state) (completely in order to stop the freedom of movement, according to the fixed position slightly, and has a tendency to make molecular arrangement of formal model of a kind of phenomenon. As judging the appearance of these two types of plastic standard visual transparency of thick wall of plastic, plastic parts, general crystalline plastics is not transparent or translucent (e.g., POM, etc.), amorphous plastic is transparent, such as PMMA, etc.). In the mold design and should be paid attention to when selecting injection molding machine of crystalline plastics has the following requirements and matters needing attention.
(1) temperature rise to molding temperature required more calories, plasticizing capacity of equipment.
(2) gives off heat cooling when back to big to sufficient cooling.
(3) the density difference between molten and solid, molding shrinkage, prone to shrinkage cavity and porosity.
(4) cooling fast, low crystallinity, shrink, and high transparency. And crystallinity of the plastic parts wall thickness, wall thickness, slow cooling, high crystallinity, shrinkage, good physical properties. So crystalline plastics should die temperature must be controlled as required.
(5) the anisotropic significantly, the internal stress is big. After stripping of crystallization molecules tend to continue to crystallization, is in a state of energy imbalance, prone to deformation and warping.
6 narrow crystallization temperature range, easy happening not molten material not injection mould or jam the feed.
(4) the heat-sensitive plastic and easy hydrolysis plastic
Heat-sensitive refers to some plastic on the thermal sensitive, heated at high temperature for a long time, or the inlet cross section is too small, the shear effect, the material temperature prone to the tendency of discoloration, degradation and decomposition, with the characteristics of plastic called heat-sensitive plastic. Hard PVC, such as poly (vinyl chloride, vinyl acetate copolymer, POM, polytrifluorochloroethylene, etc. Heat-sensitive plastic in decomposed monomer, gas and solid by-products, especially some decomposition gas stimulation to the human body, the equipment, mould has, corrosion effect or toxicity. Mould design of injection molding machine and molding, therefore, should pay attention to, should choose screw injection molding machine, pouring system section should be big, mold and cylinder should be chrome plated, shall not be sluggish, must strictly control the molding temperature, also can add stabilizer in plastic, reduce its thermal performance. From plastic (such as PC) even contain small amounts of water, but can also occur under high temperature and high pressure decomposition, this performance is called easy hydrolysis resistance, this must be dry heating in advance.
(5) the stress cracking, and melt fracture
Some plastic is sensitive to stress, easy to produce internal stress and qualitative fragile easy to crack when molding, plastic pieces under the action of external force or under the effect of solvent or cracking phenomenon. Therefore, in addition to the raw material in adding additives to improve the cracking resistance, dry, should pay attention to in the raw material processing conditions, reasonably choose to reduce internal stress and increase the crack resistance. And should choose the reasonable shape of plastic parts, unfavorable setting insert and other measures to try to reduce stress concentration. When the mould design should increase draft, choose reasonable inlet and ejection mechanism, should be appropriately adjust the molding temperature, mold temperature, injection pressure and cooling time, try to avoid plastic parts with a cold short demoulding, after molding plastic parts is also appropriate for reprocessing increase cracking resistance, stress relief and prevent contact with the solvent. When a certain flow rate of polymer melt under constant temperature through the nozzle hole when its velocity exceeds a certain value, the melt surface apparent transverse crack, known as the melt fracture, parts surface and damage to property. Therefore, when choosing high polymer melt flow rate, should increase the nozzle, sprue, inlet section, reduce the injection speed, increase temperature.
(6) thermal performance and cooling rate
All kinds of plastic have different heat capacity, thermal conductivity, thermal deformation temperature, thermal properties, etc. High specific heat capacity of the plasticizing need quantity of heat, should choose plasticizing capacity of large injection molding machine. High heat distortion temperature, plastic mold release early, cooling time is short, but to prevent cooling after demoulding deformation. Low thermal conductivity of the plastic cooling speed slow (such as ion polymer cooling speed is very slow), therefore, must be cooled sufficiently, to strengthen the mold cooling effect. Hot runner mould is suitable for the low heat capacity, high thermal conductivity of plastic. Large heat capacity, thermal conductivity, low thermal deformation temperature is low, slow cooling rate of the plastic is not conducive to high-speed molding, must choose the proper injection molding machine and strengthen the mold cooling. All kinds of plastic, according to the requirements of the species characteristics and shape of the plastic parts must be kept in proper cooling speed. So the mould must be set up according to the requirements of molding, heating and cooling system to maintain a certain temperature. When high mold temperature should be cool, to prevent the plastic deformation after demoulding, shorten the molding cycle, lower crystallinity. When plastic waste heat is not enough to make the mold to keep a certain temperature, the mould should be equipped with heating system, to keep the mold in a certain temperature, cooling rate to control, ensure the liquidity, improve the filling conditions, or to control parts make its slow cooling, prevent the thick wall plastic parts inside and outside the uneven cooling and improve the degree of crystallinity, etc. Of good liquidity, forming area is large, the uneven temperature is according to the plastic molding, heating or cooling used interchangeably or sometimes local heating and cooling. For this mould should be equipped with corresponding cooling or heating system
(7) moisture absorption
With various additives in plastic, make its in water have different degree of personal relationship, so the plastic can be roughly divided into hygroscopic, adhesion, moisture and non-absorbent adhesion moisture not easily also two kinds, material moisture content must be controlled within the scope of the permit, or under high temperature and high pressure water into gas or hydrolysis, the resin foam, less liquidity, poor appearance and mechanics performance. So hygroscopicity plastic must adopt appropriate heating methods according to the requirement and specification of preheating, when use to prevent moisture absorption.
© Copyright: 2025 Lanson Precision Intelligence Equipment Technology Co., Ltd All Rights Reserved.